Abstract
This paper proposes a new iso-parametric tool path generation scheme for trimmed parametric surface based on two discrete parameterization techniques, namely, the Partial Differential Equation method and the newly developed “Boundary Interpolation method”. The efficiency of the scheme is measured in terms of path length and computational time for machining some typical surfaces. The side-steps and forward-steps have been formulated to suit the discrete nature of the surface representation. Conventionally the forward-step is calculated by approximating the cutting curve with osculating circle. Due to this approximation there is a possibility that the tolerance can go beyond given limit. In this paper an improved tolerance constraint method has been presented to keep the tolerance in forward-step under given value by considering the true profile of the cutting curve. Case studies show that the method presented here significantly improves the path profile by maintaining the tolerance limit.













Similar content being viewed by others
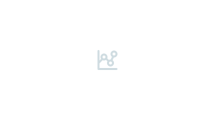
References
Elber G, Cohen E (1994) Toolpath generation for freeform surface models. Comput Aided Des 26(6):490–496
Suresh K, Yang D (1994) Constant scallop-height machining of free-form surfaces. ASME J Eng Ind 116(2):253–259
Ding S, Yang DCH, Han Z (2005) Boundary-conformed machining of turbine blades. Proc IMechE Part B J Eng Manuf 219(3):255–263
George KK, Babu NR (1995) On the effective tool path planning algorithms for sculptured surface manufacture. Comput Ind Eng 28(4):823–836
Huang Y, Oliver JH (1994) Non-constant parameter NC tool path generation on sculptured surfaces. Int J Adv Manuf Technol 9(5):281–290
Li CL (2007) A geometric approach to boundary-conformed tool path generation. Comput Aided Des 39(11):941–952
Li H, Feng HY (2002) Constant scallop-height tool path generation for three axis sculpture surface machining. Comput Aided Des 34(9):647–654
Loney GC, Ozsoy TM (1987) NC machining of free form surfaces. Comput Aided Des 19(2):85–90
Zhang LP, Nee AYC, Fuh JYH (2004) An efficient cutter contact curve tool path regeneration algorithm for sculptured surface machining. Proc IMechE Part B J Eng Manuf 218(4):389–402
Sarkar S, Dey PP (2013) Tool path generation for algebraically parameterized surface. J Intell Manuf. doi:10.1007/s10845-013-0799-x
Lin RS, Koren Y (1996) Efficient tool-path planning for machining free-form surfaces. J Eng Ind ASME Trans 118(1):20–28
Lasemi A, Xue D, Gu P (2010) Recent development in CNC machining of freeform surfaces: a state of the art review. Comput Aided Des 42(7):641–654
Sarkar S, Dey PP (2012) A new boundary interpolation technique for parameterization of planar surfaces with four arbitrary boundary curves. Proc IMechE Part C J Mech Eng Sci 227(6):1280–1290
Hsu K, Lee SL (1992) A numerical technique for two-dimensional grid generation with grid control at all of the boundaries. J Comput Phys 96(2):451–469
Westgaard G, Nowacki H (2001) Construction of fair surfaces over irregular meshes. ASME. J Comput Inf Sci Eng 1(4):376–384
Cebeci T, Shao JP, Kafyeke F, Laurendeau E (2005) Computational fluid dynamics for engineers. Horizons Publishing Inc., California
Thompson JF, Warsi ZUA, Mastin CW (1985) Numerical grid generation, foundations and applications. North Holland
Hoffmann KA, Chiang ST (1989) Computational fluid dynamics for engineers. Engineering Education System, USA
Vladimir DL (2010) Grid generation methods. Springer, New York
Marsh D (2005) Applied geometry for computer graphics and CAD. Springer, London
Yamaguchi F (1988) Curves and surfaces in computer aided geometric design. Springer, London
Sarkar S, Dey PP (2013) A new Iso-parametric machining algorithm for free-form surface. Proc IMechE Part E J Process Mech Eng. doi:10.1177/0954408913495191
Faux ID, Pratt MJ (1979) Computational geometry for design and manufacture. Ellis Horwood Limited, Chichester
Stoker JJ (1989) Differential geometry. Wiley-Interscience, New York
Hanta A, Grieve B (2000) Cartesian machining versus parametric machining: a comparative study. Int J Prod Res 38(13):3043–3065
Author information
Authors and Affiliations
Corresponding author
Rights and permissions
About this article
Cite this article
Sarkar, S., Dey, P.P. Tolerance constraint CNC tool path modeling for discretely parameterized trimmed surfaces. Engineering with Computers 31, 763–773 (2015). https://doi.org/10.1007/s00366-014-0388-4
Received:
Accepted:
Published:
Issue Date:
DOI: https://doi.org/10.1007/s00366-014-0388-4